Securing the Last Mile – Cold Chain Visibility for Retail and Consumer Shipments
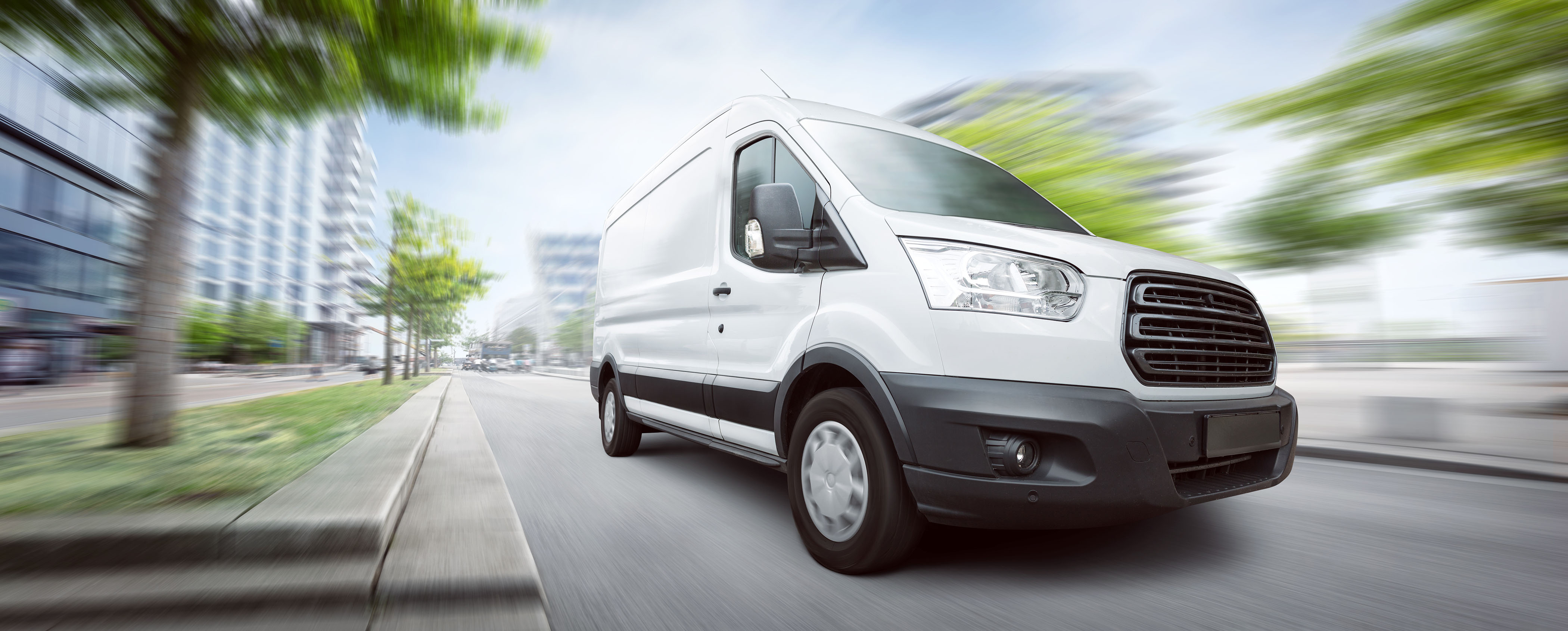
Background
The standard for temperature monitoring in cold chainapplications such as pharmaceuticals is the passive temperature tag. Devicesare activated by the sender, usually by pressing a button, and then included inthe package being shipped. When the package is received, the tag is read by therecipient (usually using a PC with a USB port), checked for temperatureexcursions, and uploaded or emailed for future reference.
This process, although cumbersome, generally suffices for partsof the cold chain where the receiver bears responsibility for the integrity ofthe shipment, and has a vested interest in ensuring that temperature excursionsare identified and addressed. For example, pharma shipments from contractmanufacturers to their customers, where the customer is maintaining strictinbound quality control, can use traditional passive tags without much difficulty.
The Problem
Passive tags, however, don’t do particularly well insituations where the sender, rather than the recipient, has responsibility forthe chain of custody. Examples of this include distributor shipments ofperishables to retail stores and vaccine deliveries to remote villages. Theserecipients typically have someone receiving the shipment who can check the tagfor a simple go/no go indicator, but plugging in a USB, checking excursions,and uploading or sending data files is likely to be a “bridge too far”.
Real-time Tags?
Real-time tags that use cellular communications offer onealternative, since they transmit data continually (as long as coverage exists)and thus provide the sender with temperature data up to the point of delivery.Unfortunately, situations where the sender is the responsible party tend to nothave a well-developed reverse logistics path, so that recovery and reuse of thedevices is problematic. Since real-time cellular monitors are, for the moment,prohibitively expensive to be single-use, they aren’t suitable for the final legof the cold chain.
Temperature Indicators
With USB data loggers being too cumbersome for most “lastmile” applications, and real-time loggers being too expensive, many cold chainmanagers have had to rely on single-use temperature indicators, often referredto as “go no-go strips”. These are simple to use, with a simple “is the circlefilled in” user interface. They’re also inexpensive, making them well-suited toretail and consumer shipments.
Unfortunately, temperature strips have somesignificant disadvantages. Since they’re not actual loggers, they don’t recordany history, aren’t configurable, and don’t allow for any cloud connectivity or evendata retention. Most importantly, there is no way to determine whether the indicatorhas been checked.
The Seguro Solution – “Smart Passive”
In Seguro’s “outbound” model, the workflow is flipped, and thesetup of the logger is handled by the sender. The receiver only needs to tapthe logger with any smartphone, and they see a complete history of the shipment,as well as automatically upload the history to the cloud. They don’t even needto have a special app on their phone.
There are a lot of advantages to this model, obviously. Forthe receiver, there is the opportunity to get a full temperature history forthe shipment, rather than a simple dot on a paper strip. They can even save oremail the history for future reference, and have access to attached files, suchas an MSDS or use instructions.
For the sender, gaining visibility into the last leg of thecold chain is a huge benefit. As well as receiving positive confirmation of successfulshipments, the sender has instant knowledge of potential problems, and can proactivelyfollow up with the customer. And, since the full history is available in thecloud in a variety of formats, there’s the opportunity to analyze history dataand look for ways to improve the integrity of these last mile shipments.
Scenarios
To illustrate the power of an outbound workflow using Seguro’ssmart passive monitors, let’s look at some specific examples. In all of thesecases, current logger solutions are either insufficient or cost-prohibitive, sotemperature monitoring is either not done at all, or done using basictemperature strips.
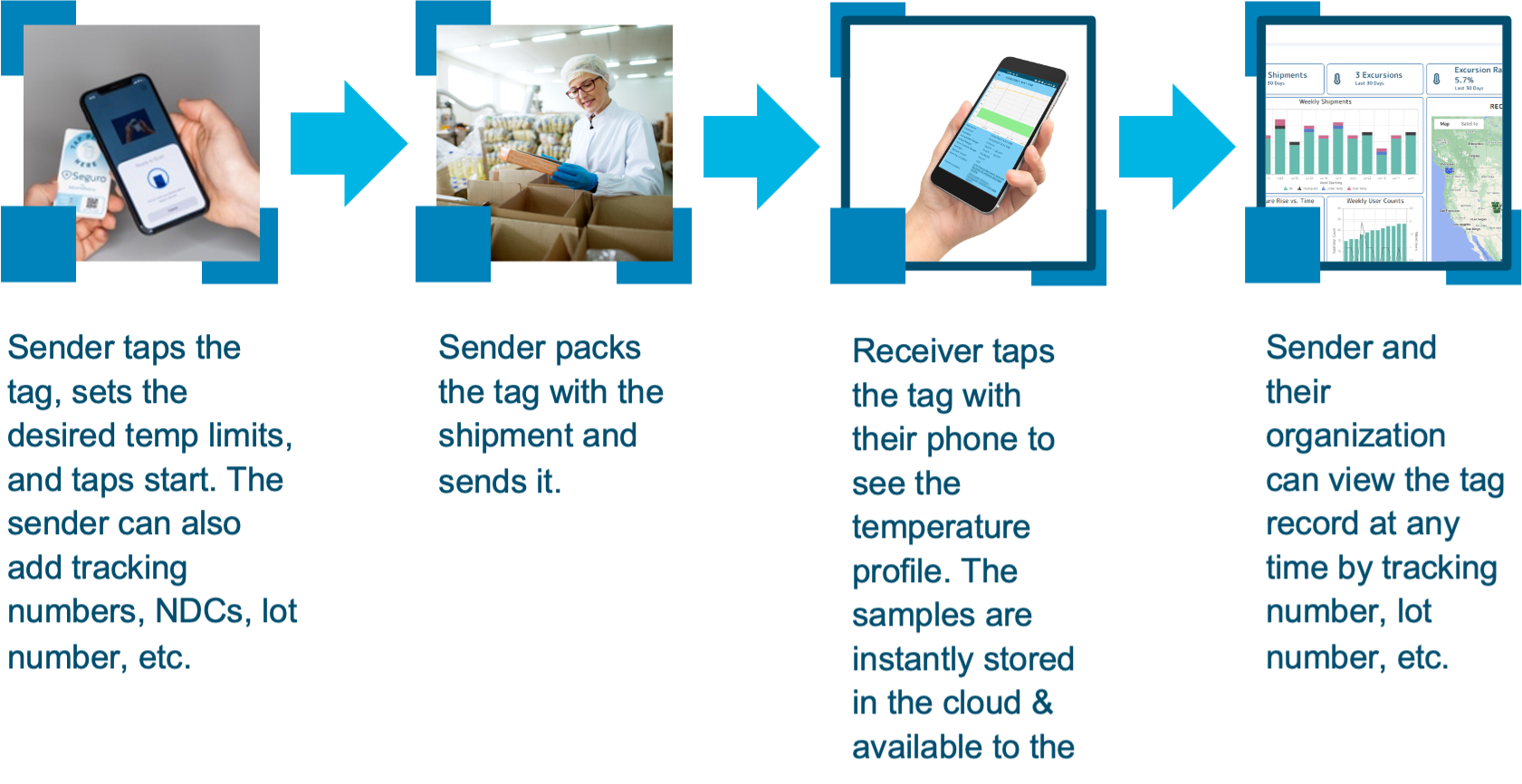
Scenario 1: Distribution to Physician Office
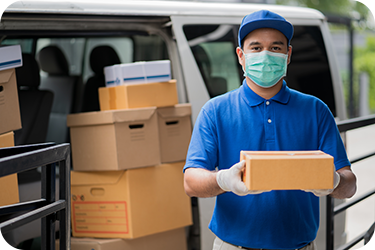
When we talk about last-mile temperature monitoring, thescenario that most often comes to mind is deliveries to physician offices. Here,we find no shortage of highly trained staff, from doctors and nurses to techniciansand admin staff. That being said, the staff is also extremely busy, and focused(rightfully so) on patient care. Any cold chain monitoring needs to be fast,simple, and foolproof, and often this means resorting to basic temperaturestrips.
Using smart passive loggers provides much-needed visibilityto this last leg of the cold chain. Here, the trained logistics staff at the distributorstarts the logger, after setting thresholds, and adding information such astracking number and invoice, and even taking a photo of the shipment.
When the admin staff at the physician’s office receives theshipment, they simply tap the logger with their phone, and the temperaturehistory for the shipment is displayed. At the same time, the data is sent tothe cloud, and the distributor is notified if there are any temperatureexcursions that need to be investigated.
Advantages for the distributor:
· Positive confirmation of a secure cold chain
· Automatic cloud storage for future reference
· Automatic alerts on temperature excursions
Advantages for the customer:
· Simple, mobile-based interface
· Full temperature history
· PDF record for future reference
Scenario 2: Farm to Retail Berry Shipment
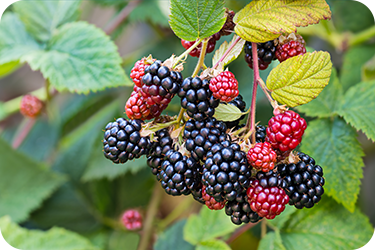
Berries. We all have our favorites, and they’re great witheverything from waffles to daiquiris. They’re also one of the most challengingproducts for cold chain managers, due to their narrow temperature range, shortshelf life, and fragile structure. Because of their fragility, it’s importantto minimize handling, and many fresh market berries have only two handlingsteps: harvest and final consumer use. Fruit are harvested directly into theirfinal container, graded in the field, and packed directly into a precooled refrigeratedtruck bound for a cold chain distribution center. From there, they are usuallyshipped directly to retail locations, with the total farm-to-consumer timebeing anywhere from five to ten days.
In addition to fast-as-possible logistics requirements,berries also have an unusually narrow temperature range requirement duringshipping. As an example, strawberries should be maintained at between zero andone degree Celsius. Colder temperatures can damage the fruit, while warmertemps can reduce their shelf life, as well as increasing condensation, which promotesmold growth.
Temperature monitoring in berry applications is challenging becausethere are limited touch points between the harvest and the retail store. Temperatureloggers are already used in many cases between the field and the packagingpoint, where the berries are palletized. At this point, though, visibility islost. With USB-based loggers being too difficult to use at the retail point,the last leg of the cold chain, which is usually the most challenging, oftengoes unmonitored.
Using smart passive loggers gives the logistics manager achance to reclaim lost visibility. In the field, the grower starts the loggerrecording by pressing the button on the logger. At the distribution center, thelogistics staff can read the temperature history so far, and attach usefulinformation such as grower identity, batch number, etc.
At this point, the temperature history is automaticallystored in the cloud, and the logistics staff can retrieve the full record atany point in the future. They can then return the logger to the shipment forthe next and final leg of the journey.
When the shipment arrives at the retail location, theshipping staff can retrieve the full temperature record from harvest with asimple tap of a smartphone. The same history is automatically stored in thecloud, and available to the logistics staff at the distribution center.
Advantages for the grower:
· Simple start interface
· Compact form factor
Advantages for the distributor:
· Positive confirmation of a full secure coldchain
· Automatic cloud storage for future reference
· Automatic alerts on temperature excursions
Advantages for the retail store:
· Simple, mobile-based interface
· Full temperature history
· PDF record for future reference
Scenario 3: Pharmaceutical Shipment to Consumer
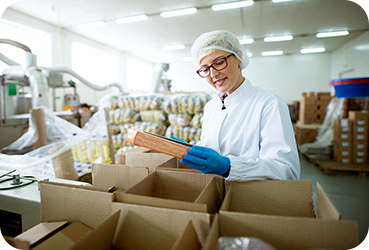
Over the last ten years, direct delivery of pharmaceuticalsto consumers has become a large part of pharma market, driven by the growth ofonline retail in other markets, and continued consolidation and efficiencygains in the pharma industry. The COVID-19 epidemic only accelerated thistrend, with patients, many of whom were immunocompromised, needing alternativeways to obtain prescriptions.
Direct-delivery drug retail often involves cold chainrestrictions, and while the temperature ranges are usually not as narrow asthose for berry and other fresh market deliveries, the cost of spoilage is muchhigher, with shipments to a single consumer often costing thousands of dollars.
At the same time, consumers are both unwilling and (in somecases) unable to plug in a USB logger to a PC, download the data, and send afile, which means that the only “logging” that can be done for consumershipments is with single-use temperature indicator strips.
Smart passive loggers offer an alternative in many cases. Tobe sure, some consumers, particularly some in the demographic receiving homepharma shipments, would be challenged by an interface that requires asmartphone. But as smartphone use becomes more common in an aging population,this will become less of an issue.
Here again, the trained logistics staff at the distributorstarts the logger, after setting thresholds, adding information such astracking number and instructional videos, and even taking a photo of theshipment. Including a card or note with instructions for first-time users willsignificantly increase the consumer engagement rate.
When the consumer receives the shipment, they simply tap thelogger with their phone, and the temperature history for the shipment isdisplayed. At the same time, the data is sent to the cloud, and the distributoris notified if there are any temperature excursions that need to beinvestigated.
Advantages for the distributor:
· Positive confirmation of a secure cold chain
· Automatic cloud storage for future reference
· Automatic alerts on temperature excursions
Advantages for the consumer:
· Simple, mobile-based interface, with no apprequired
· Full temperature history gives betterpeace-of-mind than a temperature strip
Conclusion
Traditional monitoring technologies work well forintermediate parts of the cold chain, where trained personnel are available atthe receiving end of the shipment. For “last mile” deliveries, though, temperaturestrips, USB loggers, and cellular loggers all have significant drawbacks. Ironically,the last mile is often the most tenuous part of the cold chain from atemperature security standpoint, making monitoring even more critical.
Smart passive loggers offer a modern, low-effort alternativethat is ideally suited for applications where the receiving party lacks thetraining or time to participate in true data-driven cold chain management.Here, we’ve examined three common last mile scenarios, and seen how smartpassive monitors can be used to “close the loop” on the last mile. These are,of course, merely examples, and many other applications exist in food, dairy,skin care, and pharma cold chain.
If you’re looking to close the loop on your cold chain andbring security and peace of mind to your clients and customers, let us know. Wecan help you implement a solution that fits your requirements and workflow, withoutany additional effort for your customers.